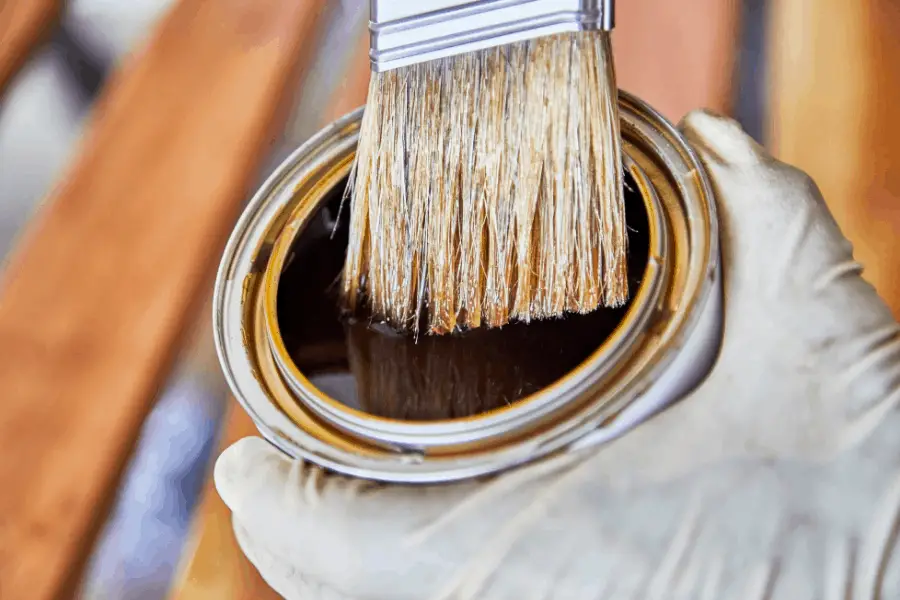
There are so many helpful options when it comes to wood finishes for your project. Each finish has a specific purpose and function that separates it from the others. I’ve researched through the internet and put together a summary on the different types of wood finishes.
What are the different types of wood finishes? Drying Oils, Rubbing Oils, Shellacs, Lacquers, Varnishes, Polyurethanes, Epoxies, Waterborne Acrylics, Oil Paints, Latex Paints, Stains, Wood Dyes, Wood Fillers, Sanding Sealers, and Waxes.
Keep reading below to learn more about wood finishes.
What Are The Different Types Of Wood Finishes?
To finish a project safely and successfully, it helps to understand how finishes work. Although this is a complex subject, the basics are fairly straightforward. Despite the myriad of finishing choices that overwhelm you in every hardware store, there are more similarities between finishes than there are differences.
Take a few minutes to read the labels on a half-dozen cans of finishes and you’ll find that different brands even different types of finishes use many of the same chemicals blended in slightly different proportions.
You simply need to know what these chemicals are and how they react with wood. You must also understand how they react with you, and how to protect yourself from their harmful effects. Finishes are toxic materials. If used prudently, with the recommended precautions, they are relatively safe. Improperly used, however, finishes can cause discomfort, disability, even death.
Comparing the ingredients and divining the dangers in a few cans of finish presume, of course, that you will be able to find cans whose labels list the contents. This is becoming increasingly difficult.
Walk into any hardware store or thumb through a finishing catalog, and you’ll likely find these different types of wood finishes:
Drying Oils: boiled linseed oil, pure tung oil.
Rubbing Oils: Danish oil, antique oil, most “tung oil” finishes, salad bowl finish.
Shellacs: white shellac, orange shellac.
Lacquers: spray lacquer, brush lacquer, lacquer paint.
Varnishes: tung oil varnish, spar varnish, varnish stains.
Polyurethanes: polyurethane varnish, urethane stain.
Epoxies: bar top finish, epoxy resin.
Waterborne Acrylics: water-based varnish, water-based lacquer (sometimes called water reducible varnish and lacquer)
Oil Paints: spray paint, house paint, artist’s oils.
Latex Paints: interior latex, exterior latex, artist’s acrylics.
Stains: oil stain, gel stain.
Wood Dyes: aniline dye, spirit stain.
Wood Fillers: paste filler, liquid filler.
Sanding Sealers: lacquer sealer, varnish sealer.
Waxes: paste wax, furniture wax.
There are many finishing materials, such as wax sticks, stick shellac, wood putty, paint strippers, and so on, that are not included here because they are not necessary parts of a finishing system. Their are various solutions you can apply to a wood surface to create a protective, attractive film.
With a few exceptions, most of these finishes hear little resemblance to the old-time concoctions of natural resins and solvents. Today, they’re made from synthetic or highly modified resins with a much higher molecular weight. The solvents, too, have been refined to make more “active” compounds needed to liquify the larger resin molecules. The advantages of these new compounds is that they are easier to apply, quicker to dry, and more durable than their forebears.
In one important respect, even the newest synthetic finishes are exactly the same as old-time formulas. They still consist primarily of resins ( sometimes referred to as “solids”) and solvents (also called “vehicles” or “carriers”) There are many other chemicals in modern finishes, of course.
For example, most include driers, heavy metal salts such as cobalt or manganese that speed the drying process. Flatteners are extremely fine white or colorless powders, often made from quartz or silica, that give the finish a flat or “satin” look.
Pigments are colored, opaque powders that tint the finish or stain. There are others that you might find listed on a label, such as binders, plasticizers, extenders, fillers, hardeners, and so on that affect the characteristics of the finish.
It’s not necessary that you know the names or even the purposes of all these additives, unless you wish to mix your own synthetic finishes from scratch. What’s important is that you understand these materials are grouped into two general categories (volatile and nonvolatile) The volatile chemicals are, for the most part the solvents. The ingredients that keep the finish liquid so you can wipe, brush, pour, or spray it on the wood.
After the finish is applied, the volatile chemicals evaporate or dissipate and what’s left is everything else. The nonvolatile resins, hardened oils, driers, flatteners, pigments, and so on. These form the resinous film.
What Are The Different Chemical Reactions For Wood Finishes?
More important than the ingredients, or even the type of finish, is how the liquid finish hardens to form a chemical film. There are four possible reactions:
- Solvent-releasing: As the solvent evaporates from the finish, it leaves the resin on the wood surface. The resin is not altered chemically; it just changes from a liquid to a solid. It can be dissolved again by applying the same solvent to it. Examples: shellacs and lacquers.
- Reactive: As the thinners evaporate, the resins or oils react with oxygen in the air. As they oxidize, they harden and change chemically. This change is permanent; the resins and oils cannot be redissolved by applying the same thinners. Examples: drying oils, rubbing oils, varnishes, polyurethanes, and oil paints.
- Catalyzing: The resins in these finishes also form films by chemical reaction. However, they don’t react with the air but with chemical catalysts. The resins must be mixed with hardeners (catalysts) for the film to form. Once the film is cured, it resists almost all solvents. Example: Epoxies.
- Coalescing: The finish consists of a resin (usually with a very high molecular weight) suspended in a nonreactive solvent (usually water). In addition, there is a small amount of a second, highly active synthetic solvent (called a “co-solvent” or a coalescent) that keeps the resin liquid. As the water evaporates, the active solvent dissolves the resin and it forms a continuous film. A coalesced film is not as impervious to solvents as reactive finishes, but it cannot be redissolved as easily as solvent-releasing types. Examples: waterborne resins, latex paints.
Pro Tip: There is a difference between finishes that harden and those that cure. Finishes in which a chemical reaction takes place, such as reactive and catalyzing finishes, cure. Solvent-releasing and coalescing finishes harden as the solvents dissipate.
In addition to forming films, finishes also form bonds with the wood and when applied in layers with themselves. There are two types of bonds:
- Chemical Bonds: The molecular structure of the film layer links with that of the wood or the previous layer. These are the strongest (and the most desirable) bonds.
- Mechanical Bonds: The finish sticks to the wood or to another finish layer much like adhesive tape, grasping surface irregularities. These bonds are often very weak.
Almost all finishes form mechanical bonds with wood; finishing chemicals do not react with lignin or cellulose, the two major chemical components of wood. For this reason, surface preparation is especially important. Ideally, the first coat of finish should penetrate the wood surface slightly, forming what finishing chemists call an “interface,” where the two materials interlock.
After the first coat, you must concern yourself with how the finish bonds to itself. Solvent-releasing finishes always form chemical bonds between coats. A newly applied coat partially dissolves the dry coat underneath it, and the two coats blend into one. Once a catalyzing finish has cured, successive coats will not chemically bond with it. Only mechanical bonds will form.
Other types; reactive and coalescing finishes form both chemical and mechanical bonds. If you apply a coat just as the previous coat has set, but before it has a chance to cure (harden completely), then the two layers form strong chemical bonds. After a coat cures, a successive coat can only form mechanical bonds.
When choosing a finish, it’s useful to know how various types form films and bonds. Finishes are often built up in several layers, and each layer may have a different chemical formula. Knowing how each layer reacts makes it easier to identify compatible finishing materials. For example, craftsmen often apply a clear finish over a stain. You don’t want the chemicals in the finish to dissolve the stain, nor do you want the stain to prevent the finish from hardening.
Almost every finish, no matter what its chemical formula, is made up of two important parts. The chemicals that form the solid chemical film are often called the nonvolatile chemicals. Those that suspend, dissolve, or somehow keep the first set of chemicals liquid until you apply them to the wood are solvents, carriers, or vehicles, called volatile chemicals. Shellac is a classic example of such a formula, the nonvolatile shellac solids are dissolved in a volatile liquid, alcohol.
After you apply the finish to the wood, the alcohol evaporates, and the solids are left behind to form a hard chemical film. Boiled linseed oil is an exception. This finish consists of just one chemical that serves both functions the oil is both the carrier and the solid. After you apply the liquid oil to the wood, it reacts with oxygen and solidifies.
As the solvent evaporates from a solvent-releasing finish, such as shellac or lacquer, the solids form a solid matrix. However, there is no molecular change and the solids can be easily dissolved again. A fresh coat of finish partially dissolves the old one, and the two coats form a chemical bond.
When they come in contact with oxygen, the resins in reactive finishes such as rubbing oils, varnishes, and polyurethanes form crosslinks, joining up in complex molecular matrices. When the reaction is complete, the solid film is molecularly different from the liquid resin and the reaction cannot be easily reversed. Consequently, the film cannot be dissolved by the same solvent that was used as the vehicle.
An additional coat chemically bonds with the preceding one only if the older coat hasn’t completely hardened; if it has, the two coats can only form weak mechanical bonds.
The resin of a catalyzing finish, such as an epoxy, reacts with a hardener (catalyst) in much the same way reactive resins respond to oxygen. The resin molecules crosslink and form complex matrices that cannot be easily dissolved. Catalyzing finishes are not normally applied in layers. If they are, the same bonding rules apply as for reactive finishes. To achieve strong chemical bonds, you must apply a fresh coat before the old one has completely cured.
In it’s liquid state, a coalescing finish is made up of resins suspending in water and small amounts of an active co-solvent. As the water evaporates, the co-solvent dissolves the resins and forms a continuous film. This film hardens completely as the co-solvent dissipates. The resulting finish is just as hard as many reacted and catalyzed films, but not as resistant to solvents. Successive coats will form both chemical and mechanical coats with preceding ones.