Subscribe to Matthew Peech on YouTube
Watch The Video To See All The Projects
Welcome to another episode of Smalls that Sell, where the host breaks down trending items from big box stores and teaches viewers how to turn them into low-cost, high-profit items. In this episode, he focuses on two trending items: galvanized sided crates and sliding shelves. The host shares his expertise on how to build these items at a super cheap price, maximizing profits for those who sell them.
The sliding shelf is a hot item that has caught the host’s attention. He highlights the importance of using hardwood for this project because the entire shelving unit is supported by the backboard against the wall and joinery in the corners. The host breaks down the most common style of the sliding shelf, which has three boards running horizontally and a slim vertical frame. He also emphasizes the importance of joinery, which is a cornerstone of the build.
Key Takeaways
- Trending items like galvanized sided crates and sliding shelves can be built at a super cheap price, maximizing profits for those who sell them.
- When building a sliding shelf, it is important to use hardwood and pay attention to joinery, which is a cornerstone of the build.
- With a couple of jigs and a little bit of creativity, you can pump out sliding shelves and blow your competition away.
Galvanized Sided Crate Teaser
In this episode of Smalls that Sell, the host introduces a new trending item that is in high demand, the galvanized sided crate. The crate is currently being sold at a high price, but the host promises to teach viewers how to build it for a low cost and maximize profits.
The galvanized sided crate is a sliding shelf that is adjustable, with each shelf being 3/4 inch thick, 16 inches long, and 5 inches wide. The frame of the shelf is made of 2 and 1/2 inch material that is 3/4 inch thick, and it is crucial to use hardwood for the frame since the entire shelving unit is supported by the backboard against the wall and the joinery in the corners.
The most important part of the build is the joinery, which is a single tooth box joint that provides a strong joint for the build. The unit is 25 inches tall and 6 inches deep, and the shelves slide back and forth in 3/4 inch notches cut into the inner sides of the boards.
To make the build, viewers can use hardwood such as oak, cherry, or walnut, and can use a dato stack, a table saw jig, or a circular saw to make the necessary cuts. The host encourages viewers not to be discouraged if they don’t have the specific tools and to use basic hand tools to figure it out.
Overall, the galvanized sided crate is a medium-sized build that is easy to make and can be sold for a high profit. Viewers can use their creativity to add contrast to the shelves and can secure the unit to the wall using screws or dowels to ensure stability.
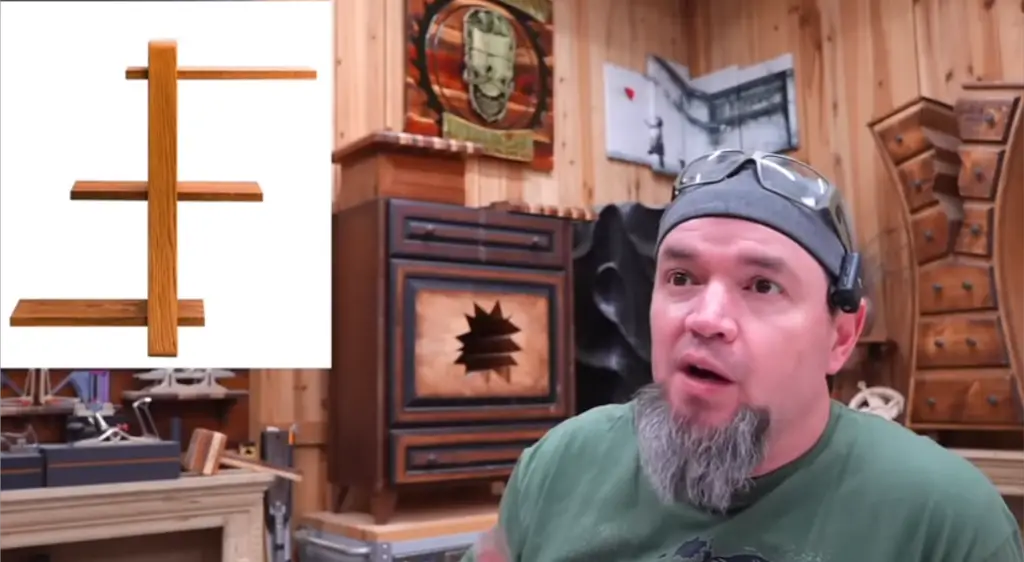
Trending Item Alert: Sliding Shelf
The host of Smalls that Sell has identified a new trending item: the sliding shelf. This item has been seen on several different sites, which is a red flag for a super hot item. The sliding shelf is a shelving unit with adjustable shelves that can be made for a super cheap price.
The sliding shelf is a medium-sized build that is super easy to make. However, it is important to note that a softwood like Pine or Picket is not recommended for this build. Instead, a hardwood like Oak, Cherry, or Walnut should be used because the entire shelving unit is being supported by the backboard against the wall and joinery in the corners.
The most common style of the sliding shelf has three boards running horizontally with a slim vertical frame. Each shelf is 3/4 of an inch thick, 16 inches long, and 5 inches wide. The frame is made out of 2 and 1/2 inch material that is 3/4 of an inch thick. The most important part of this build is the joinery, which looks like a type of single tooth box joint right on the very ends.
Before assembling the sliding shelf, notches need to be cut on the 25-inch boards that the shelves will slide into. The notches are 3/4 of an inch deep and are cut into the inner sides of these boards. The shelves are then slid into these notches to give them the ability to be adjusted.
The sliding shelf can be made with basic hand tools like a circular saw and a framing square. The cost of making this item will depend on where the wood is sourced from, but it is guaranteed to be much cheaper than the average price of $250 for a pre-made sliding shelf. With a couple of jigs and a little bit of creativity, anyone can make these babies and blow their competition out of the water.
[Guide] How To Launch Your Woodworking Business For Under $1000
Click Here To View
If you’re considering turning your woodworking hobby into a part-time business check out this helpful guide on how to get started.
Shelf Build Breakdown
In this episode of Smalls that Sell, the host breaks down the trending sliding shelf, which is a medium-level build that can be made for a fraction of the cost of the retail price. The sliding shelf is a hardwood shelving unit that is supported by the backboard against the wall and the joinery in the corners. The most common style has three boards running horizontally with a slim vertical frame.
The shelving boards are made of the same material as the support frame, but the host suggests using a contrasting material for the shelves to add some visual interest. Each shelf is 3/4 inch thick, 16 inches long, and 5 inches wide.
The frame is the most important part of the build and is made of 2 and 1/2 inch material that is 3/4 inch thick. The joinery used is a type of single tooth box joint that is strong and provides ample support for the entire unit. The frame measures 25 inches tall and 6 inches deep.
To assemble the frame, the host recommends cutting the notches on the 25-inch boards that the shelves slide into. These notches are cut 4 inches from the top, 4 inches from the bottom, and 1 inch from the center. A table saw sled or miter gauge can be used to make these notches, or a circular saw can be used with a framing square to keep the blade straight.
Once the notches are cut, the frame can be glued up on its ends, and a screw or dowel can be added for extra support. The host suggests pre-drilling a hole in each of the notches on the board that will be mounted against the wall to secure the unit in place.
Overall, the cost of the build will depend on the type of wood used, but it is guaranteed to be much less than the $250 retail price. With a few jigs and a little creativity, these sliding shelves can be easily mass-produced and sold for a high profit.
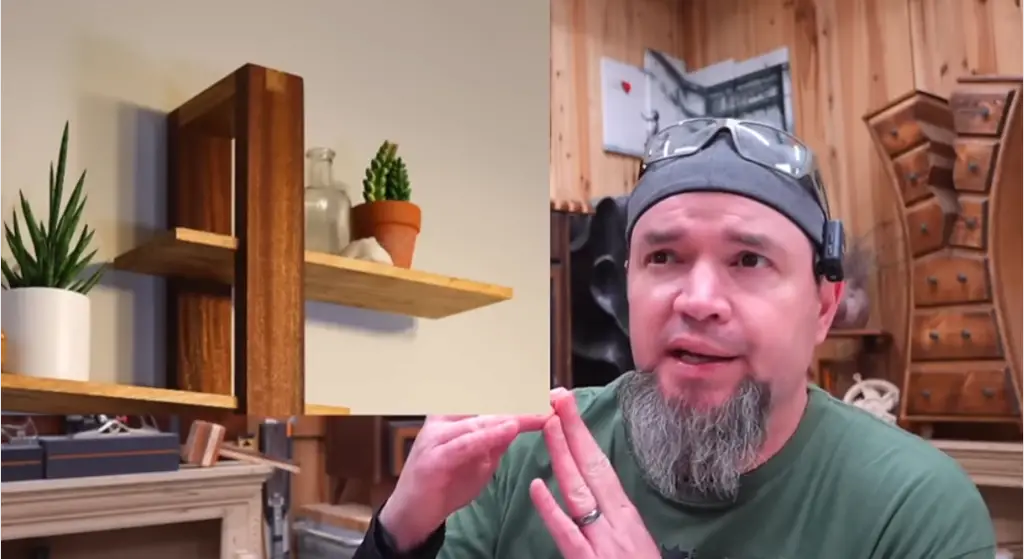
Choosing the Right Wood
For the sliding shelf project, it is important to choose the right type of wood. Softwoods such as pine or picket are not recommended for this project as they do not provide enough support for the entire shelving unit. Instead, a hardwood such as oak, cherry, or walnut should be used.
The shelves themselves do not necessarily need to be made of hardwood as they are supported by the hardwood frame. However, for aesthetic purposes, using a contrasting material for the shelves can add visual interest to the finished product.
When building the frame, it is recommended to use 2 and 1/2 inch material that is 3/4 of an inch thick. This provides ample support for the shelving unit, which is being supported by the backboard against the wall and the joinery in the corners.
The most important part of the build is the joinery, which should be a type of single tooth box joint. This joint is strong and provides the necessary support for the entire unit. To make the joint, a dado stack or a table saw jig can be used. Alternatively, the joint can be cut by hand and squared up with a chisel.
Overall, the cost of the project will depend on the type of wood used, but it is guaranteed to be much less than the average price of $250 for a pre-made sliding shelf. With a bit of creativity and some basic tools, anyone can build this project and sell it for a high profit.
Shelf Dimensions and Material
In this episode of Smalls that Sell, the host breaks down the construction of a trending item known as a sliding shelf. The shelves are adjustable and made of hardwood, which is necessary to support the weight of the entire unit. The most common style of this shelf has three horizontally running boards and a slim vertical frame.
The shelves are 16 inches long, 5 inches wide, and 3/4 of an inch thick. The frame is made of 2.5-inch material that is 3/4 of an inch thick. The joinery is a single-tooth box joint, which is a strong joint that ensures the stability of the unit. The shelf is 25 inches tall and 6 inches deep.
To make the frame, the top and bottom boards need to have a 3/4 inch tab or tongue in the center. The front and back boards need to be the full 25 inches long, while the top pieces need to be 6 inches long. The notches for the shelves are cut into the inner sides of the 25-inch boards, 4 inches from the top, 4 inches from the bottom, and one in the center.
The shelves are slid back and forth in the notches, allowing for adjustability. The unit needs to be secured to a stud in the wall to support the weight. The cost of making this shelf will depend on the type of wood used, but it will be significantly less than the average price of $250 for a store-bought shelf.
The host encourages viewers not to be discouraged if they don’t have the specific tools needed for this project. He reminds them that many modern tools have evolved from basic hand tools and encourages them to use their creativity to make their own jigs and tools.
Frame Construction Essentials
In this episode of Smalls that Sell, the host teaches viewers how to build a sliding shelf, a trending item that is currently being sold for a high price in big box stores. The sliding shelf is designed with adjustable shelves and a slim vertical frame that requires the use of hardwood for support. The most important part of the build is the joinery, which uses a type of single tooth box joint to create a strong joint for the entire unit.
To build the sliding shelf, the host recommends using 2 and 1/2 inch material that is 3/4 of an inch thick for the frame. The shelves can be made with a contrasting material to add visual interest. Each shelf is 3/4 of an inch thick, 16 inches long, and 5 inches wide. The entire unit is 25 inches tall and 6 inches deep.
To create the joinery, the top and bottom boards need to have a 3/4 inch tab or tongue in the center, while the front and back boards need to be the full 25 inches long. The joinery is created by removing material on both sides of the top and bottom boards, leaving a tongue in the center. The front and back boards are then made by using the tongue as a template and removing the material in the center. The notches for the adjustable shelves are then cut into the inner sides of the boards.
The host recommends using a box joint jig to create the joinery, but notes that it can also be done with a circular saw or hand tool. Once the joinery is complete, the unit is glued together and secured with screws or dowels. The unit should be mounted securely to a stud in the back to support the weight of the shelves.
Overall, the sliding shelf is a medium-sized build that can be made for a fraction of the cost of store-bought versions. With a bit of creativity and the right tools, anyone can build this trending item and sell it for a high profit.
Joinery: The Cornerstone of the Build
In this episode of Smalls that Sell, the host breaks down the trending item of a sliding shelf and teaches viewers how to build it for a low cost, high-profit item. The sliding shelf is unique in that each shelf is adjustable, but it requires a hardwood for support due to the backboard against the wall and the joinery in the corners.
The frame of the sliding shelf is made of 2 and 1/2 inch material that is 3/4 of an inch thick, and the most important part of the build is the joinery. The most common style uses a single tooth box joint on the ends, which is a strong joint for the build. The entire unit is 25 inches tall and 6 inches deep.
To make the joinery, the top and bottom boards need to have a 3/4 inch tab or tongue in the center, and the front and back boards need to be the full 25 inches long. The notches on the 25 inch boards that the shelves slide into are cut 4 inches from the top, 4 inches from the bottom, and one in the very center.
The shelves are made of contrasting material to the frame and are 3/4 of an inch thick, 16 inches long, and 5 inches wide. The shelves slide back and forth in the notches to allow for adjustability.
While a dato stack can make the box joint jig easier, it is not necessary. A simple table saw jig or cutting by hand and using a chisel to square everything up can also work. The sliding shelf can be mounted securely to the wall by pre-drilling a hole in each notch on the board that goes against the wall and mounting it into a stud.
Overall, the sliding shelf is a medium build that can be made for a fraction of the cost of the $250 average price for the trending item. With a little creativity and some basic tools, viewers can easily build and sell these sliding shelves for a high profit.
Cutting Notches for Adjustable Shelves
For those looking to build a sliding shelf, it’s important to note that each shelf needs to be adjustable and the frame needs to be made of hardwood to support the weight. The most common style of this shelf has three horizontal boards and a slim vertical frame.
To begin, the shelves are made of the same material as the support frame, but it’s recommended to use a contrast for the shelves. Each shelf is 3/4 inch thick, 16 inches long, and 5 inches wide.
The frame is made out of 2 and 1/2 inch material that is 3/4 inch thick. The most important part of the frame is the joinery, which is a type of single tooth box joint on the very ends. This joint is strong and provides the necessary support for the entire unit. The shelf unit is 25 inches tall and 6 inches deep.
Before assembling the frame, it’s important to cut notches on the 25 inch boards where the shelves will slide in for adjustability. These notches are 3/4 inch deep and are located 4 inches from the top, 4 inches from the bottom, and one in the center of each board.
To make the notches, a dado stack on a miter saw can be used, or a circular saw with a framing square against the edge. If these tools are not available, a hand saw and chisel can be used as a substitute.
Once the notches are cut, the frame can be glued together on the ends and secured with screws or dowels. It’s important to mount the shelf securely to a stud in the back to support the weight. Pre-drilling holes in the notches on the board that will be against the wall and attaching screws or dowels is recommended.
Overall, this sliding shelf can be built for a fraction of the cost of store-bought versions and is a great addition to any home. Don’t let the lack of fancy tools hold you back, get creative and build your own sliding shelf today!
Alternative Tools and Techniques
In this episode of Smalls that Sell, the host shares some alternative tools and techniques for building trending items from big box stores. One such item is the sliding shelf, which can be built using hardwood materials for maximum support.
The most important part of this build is the joinery, which requires a type of single tooth box joint for maximum strength. This joint can be made using a dato stack or a simple table saw jig. If you don’t have access to these tools, you can still make it work with basic hand tools.
To make the sliding shelves adjustable, notches need to be cut into the inner sides of the boards. This can be done using a miter saw or circular saw, and a framing square can help keep the blade straight.
Once the joinery and notches are cut, the shelves can be glued up and secured with screws or dowels. It’s important to mount the unit securely to a stud in the wall to support the weight of the shelves.
Overall, this build is a medium difficulty project that can be completed with a little bit of creativity and some basic tools. And the best part? It won’t cost anywhere near the $250 price tag of the store-bought version.
Assembly and Mounting
The sliding shelf is a medium build that is super easy to build. However, it requires a hardwood material for the frame and oak strips for the shelves. The entire shelving unit is supported by the backboard against the wall and the joinery in the corners, which is a very important part of the build.
To build the frame, one needs 2 and 1/2 inch material that is 3/4 of an inch thick. The most important part of the frame is the joinery, which looks like a type of single tooth box joint right on the very ends. This joint is strong enough to support the entire unit, which is 25 inches tall and 6 inches deep.
To assemble the frame, one needs to cut the notches on the 25-inch boards where the shelves will actually slide in. This gives the shelves the ability to be adjusted. The notches are cut 4 inches from the top, 4 inches from the bottom, and one in the very center.
To mount the sliding shelf, one needs to secure it in the back. One can pre-drill a hole in each one of the notches on the board that’s going against the wall and make sure to mount it into a stud. Once everything is mounted, the boards can be slid in from the end.
The cost of making the sliding shelf depends on where one gets their wood. However, it is guaranteed that no matter what type of wood one uses, it will not come anywhere near $250. With a couple of jigs and just a little bit of creativity, one can pump out these babies and blow their competition out of the water.
Cost-Effective Crafting
Looking for a way to maximize your profits on trending items? Look no further than cost-effective crafting! In this episode of Smalls that Sell, the host breaks down how to turn a hot item like a galvanized sided crate or a sliding shelf into a low-cost, high-profit product that you can put your own twist on and sell like crazy.
When it comes to building a sliding shelf, the key is to use a hardwood like oak, cherry, or walnut for the frame. The shelves themselves don’t need to be hardwood since they’re supported by the frame. Each shelf should be 3/4 of an inch thick, 16 inches long, and 5 inches wide. The frame should be made of 2 and 1/2 inch material that is 3/4 of an inch thick.
The most important part of the sliding shelf build is the joinery. The most common type of joinery for this project is a type of single tooth box joint, which is a strong joint for the build. The entire unit is 25 inches tall and 6 inches deep, with three boards running horizontally and a slim vertical frame. The shelves are adjustable thanks to 3/4 inch notches cut into the inner sides of the 25-inch boards.
To make the sliding shelf, start by cutting the joinery and the notches on the 25-inch boards. Then, glue the boards together on their ends and attach a screw or dowel to lock everything in place. Mount the shelf securely to a stud in the wall, and slide the shelves in from the end.
With just a little creativity and a couple of jigs, you can make these sliding shelves for a fraction of the cost of buying them from a big box store. So why not give it a try and see how much you can save?
Final Touches and Mounting Strategy
In this section, Matthew Peech discusses the final touches and mounting strategy for the sliding shelf project. He emphasizes the importance of using hardwood for the frame and the joinery to ensure maximum support.
The most common style of this project consists of three horizontal boards with a slim vertical frame, with each shelf being adjustable. The shelves are typically made of the same material as the support frame, but he suggests using contrast for added visual appeal.
To create the frame, he recommends using 2.5-inch material that is 0.75 inches thick, which can be found in heavy-duty pallets. The joinery is a crucial aspect of the project, with Matthew recommending the use of a single-tooth box joint for maximum strength.
Once the joinery is complete, he advises cutting notches in the 25-inch boards for the shelves to slide in. The shelves themselves are 16 inches long, 5 inches wide, and 0.75 inches thick.
To mount the shelf, hesuggests pre-drilling holes in the notches and mounting the unit securely into a stud. The weight of the shelf is transferred to the board in the back, so it is crucial to ensure that it is secure.
Matthew Peech emphasizes that the cost of the project will depend on the type of wood used, but it is guaranteed to be much cheaper than the $250 price tag of similar products. The project can be easily mass-produced with a few jigs and some creativity, making it a great low-cost, high-profit item to sell.