Subscribe to LRN2DIY on YouTube
The clutch collar is an essential component of power drills, and understanding how it works is crucial for anyone who uses power tools. In this article, the mechanics of the clutch collar will be explained, along with its settings and applications. The article will also cover the differences between an impact driver and a drill, and the importance of the clutch in delicate tasks.
The “Art Of Woodworking” Guide Plus 40 Project Plans
Click Here to Download Your Free Copy of The “Art Of Woodworking” Guide
Key Takeaways:
- The clutch collar is a crucial component of power drills, and understanding its mechanics is essential.
- The clutch settings are important for delicate tasks, such as installing cabinet hardware or pre-drilled and pre-counter sunk screws.
- The clutch was invented by Black & Decker in 1946 and has remained largely unchanged since then.
Understanding the Clutch Collar
The clutch collar is a mechanism found in power drills that allows the user to adjust the torque output of the drill. By adjusting the clutch setting, the user can prevent the drill from over-tightening or stripping screws and can also ensure that the drill does not apply too much force to delicate materials.
The clutch settings on a drill can vary depending on the manufacturer and model. Some drills have a hammer mode, a drill bit mode, and a range of clutch settings, while others only have a range of clutch settings. The clutch should only be used when driving screws or fasteners of some sort, as it is not designed for drilling holes.
To demonstrate the importance of using the clutch, the speaker in the video drives 2 1/2 inch screws into a piece of Douglas fir at each of the 11 graduations on the clutch collar. The results show that even the lightest setting on the clutch can apply too much torque, which can cause the screw to be driven too far into the material.
The clutch is particularly useful when working with smaller screws or delicate materials. For example, when installing cabinet hardware or cup hinges, the user can adjust the clutch setting to ensure that the screws are not over-tightened and that the material is not damaged.
The clutch collar mechanism works by using a spring inside the collar that compresses and gives resistance as the user turns the collar. The higher the clutch setting, the more resistance the spring provides, which limits the amount of torque the drill can apply.
It is interesting to note that the pistol grip or trigger-style drill that we know today has been around for over 100 years, but it has only been around 75 years since the clutch was invented by Black & Decker in 1946. The clutch mechanism has not changed much since its invention and is still widely used in power drills today.
In summary, the clutch collar is an essential mechanism in power drills that allows users to adjust the torque output of the drill. By understanding how the clutch works and when to use it, users can prevent damage to materials and ensure that screws are properly tightened without being over-tightened.
[Guide] How To Launch Your Woodworking Business For Under $1000
Click Here To View
If you’re considering turning your woodworking hobby into a part-time business check out this helpful guide on how to get started.
Clutch Settings and Applications
The clutch collar is an important feature of power drills that allows users to adjust the amount of torque applied when driving screws or fasteners. Different drill manufacturers have their own variations of the clutch, but the basic principle remains the same. In this section, we will explore the different clutch settings and their applications.
When to Use the Clutch
The clutch should only be used when driving screws or fasteners of some sort. It is not designed for drilling holes, which is the job of a drill bit. The clutch settings on a drill depend on the manufacturer, but most drills have a range of drive settings that can be adjusted using the clutch collar.
Clutch Settings
The clutch settings on a drill can range from 1 to 24, depending on the manufacturer. The higher the number, the more torque is applied when driving screws or fasteners. It is important to use the right clutch setting for the job to avoid damaging the material or the fastener.
Applications of the Clutch
The clutch is particularly useful when working with smaller screws or delicate materials. For example, when installing cabinet hardware or cup hinges, a lighter clutch setting should be used to avoid stripping the screw or the screw hole. Pre-drilled and pre-countersunk screws also require a lighter touch, and the clutch can help ensure a perfect fit every time.
Mechanics of the Clutch
The clutch works by using a spring inside the clutch collar to adjust the amount of torque applied when driving screws or fasteners. Different manufacturers have their own variations of the clutch, but the basic mechanics remain the same. The clutch collar can be adjusted to different settings depending on the amount of torque required for the job.
In conclusion, the clutch is an essential feature of power drills that allows users to adjust the amount of torque applied when driving screws or fasteners. Different manufacturers have their own variations of the clutch, but the basic mechanics remain the same. It is important to use the right clutch setting for the job to avoid damaging the material or the fastener.
Demonstration of Clutch Settings
Driving Screws into Douglas Fir
In this video, the speaker demonstrates the different clutch settings of a drill by driving screws into a piece of Douglas fir. The speaker shows that the clutch settings can be adjusted to provide different levels of torque, which is useful when working with different types of screws and materials.
The speaker starts by demonstrating the different clutch settings on a drill, and then shows how these settings affect the torque applied to a screw. Using a 2 1/2 inch screw, the speaker drives the screw into the Douglas fir at each of the 11 graduations on the clutch collar. The speaker notes that even at the lightest setting, the drill is putting too much torque on the screw, which is not ideal.
To demonstrate the difference in torque at different clutch settings, the speaker then uses a different drill and drives the screw into the Douglas fir at every other setting, starting at 2 and ending at 24. The speaker notes that the clutch setting should only be used when driving screws or fasteners, and not when drilling holes.
Adjusting Clutch Settings
The speaker explains that the clutch settings are useful when working with delicate screws or pre-drilled and pre-countersunk screws. For example, when installing cabinet hardware or cup hinges, a light touch is needed to avoid stripping the screw or the screw hole.
To find the right clutch setting, the speaker recommends starting with the minimal amount of torque and working up to find the sweet spot. The speaker demonstrates this by using a counter sink drill bit to drill a hole in a piece of wood, and then using the clutch to drive a screw into the hole at different settings until the screw is flush with the surface of the wood.
The speaker also shares some lesser known facts about the clutch, including that it was invented by Black & Decker in 1946 and that it has been around for over 75 years. The speaker shows the mechanics of the clutch by taking apart a drill and demonstrating the spring inside the clutch collar that provides resistance when turning the collar.
Overall, the demonstration of clutch settings shows the importance of adjusting the torque when working with different types of screws and materials, and the usefulness of the clutch settings in achieving the right level of torque.
Impact Driver Versus Drill
The clutch collar is an essential component of a drill that allows the user to adjust the torque output. The clutch settings vary depending on the drill, but they typically range from 1 to 24. The clutch collar is designed to be used when driving screws or fasteners of some sort, such as lag bolts or screws. It is not meant to be used when drilling holes.
On the other hand, an impact driver is specifically designed for driving screws, tightening and loosening bolts, and other similar tasks. It is not recommended for drilling holes, but some users find that it can be used for a variety of tasks.
When it comes to using the clutch collar, there are some circumstances in which it can be particularly useful. For example, when working with smaller screws, such as those used for cabinet hardware or cup hinges, it is important to use a lighter clutch setting to avoid stripping out the screw or the screw hole. Pre-drilled and pre-countersunk screws also require a lighter touch, and the clutch can be used to ensure that the screw is driven in just the right amount.
It is worth noting that the clutch collar has been around for over 75 years, having been invented by Black & Decker in 1946. The design has changed very little since then, and it remains an essential component of most drills on the market today.
In comparison, the impact driver is a relatively new invention, but it has quickly become a popular tool among DIY enthusiasts and professionals alike. While it may not be suitable for all tasks, it is a versatile tool that can make many jobs easier and more efficient.
Overall, the choice between an impact driver and a drill will depend on the specific task at hand. For driving screws and fasteners, the clutch collar on a drill is a must-have feature. However, for tasks that require more power and speed, an impact driver may be the better choice.
Importance of the Clutch in Delicate Tasks
The clutch collar is an essential feature of power drills that enables users to control the amount of torque applied to screws and fasteners. It is particularly useful when dealing with delicate tasks that require a light touch, such as installing cabinet hardware or pre-drilled and pre-counter sunk screws. The clutch settings on a drill can vary depending on the manufacturer, but they generally offer a range of drive settings and graduations for controlling torque.
One of the lesser-known facts about the clutch is that it was invented by Black & Decker over 75 years ago and has remained a fundamental feature of power drills ever since. Despite its longevity, the clutch is still a valuable tool for DIY enthusiasts and professionals alike.
Using the clutch correctly can prevent damage to screws, fasteners, and the surrounding material. For example, when installing cabinet hardware, it is important to use a light touch to avoid stripping the screw or the screw hole. Similarly, pre-drilled and pre-counter sunk screws require a minimal amount of torque to ensure a perfect fit.
The clutch collar is also useful for controlling torque when dealing with smaller screws that do not require full bore torque. By adjusting the clutch setting to a lower level, users can ensure that the screw is driven in without damaging the surrounding material.
To fully understand how the clutch works, it is helpful to take a closer look inside the drill. The clutch collar contains a spring that compresses and provides resistance as the collar is turned. This resistance controls the amount of torque applied to the screw or fastener.
In conclusion, the clutch collar is an essential feature of power drills that enables users to control the amount of torque applied to screws and fasteners. It is particularly useful for delicate tasks that require a light touch, such as installing cabinet hardware or pre-drilled and pre-counter sunk screws. By using the clutch correctly, users can prevent damage to screws and the surrounding material, ensuring a perfect fit every time.
Want To Improve Your Woodworking?
Discover 1,000 Hours Of Step-By-Step Woodworking Videos
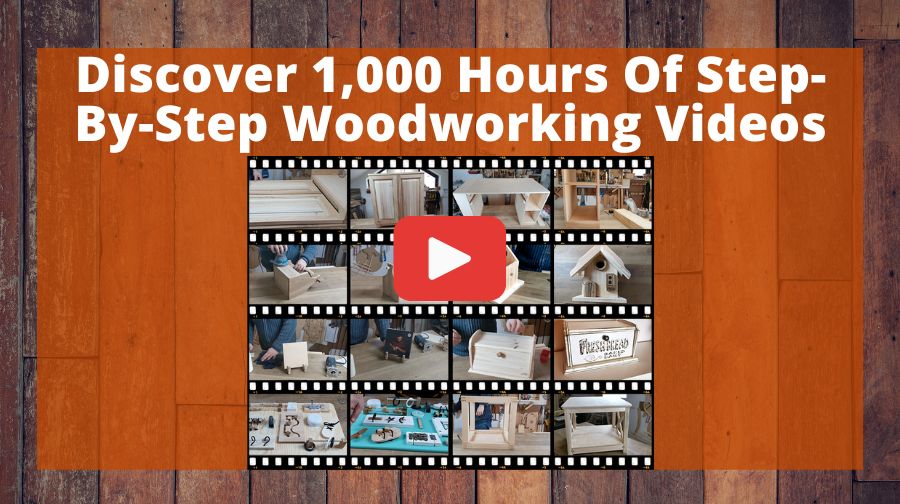
It’s called Woodwork101. A database of detailed videos and blueprints in crystal clear, mouth-watering HD that will take you by the hand and show you that DIY home projects done the right way are easy, fun, and always of top quality… turning dream into reality in a heart-beat. Getting you that perfect build each and every time.
Finding the Right Clutch Setting
Working with Small Screws
One important reason to use the clutch is when working with small screws. Using too much torque can easily strip out the screw or the screw hole. For instance, when installing cabinet hardware or cup hinges, it is important to use a lighter clutch setting to avoid overdoing it. By starting with the minimal amount of torque and working up to find the sweet spot, the clutch can ensure the screw is driven in just enough without causing damage.
Installing Cup Hinges
Cup hinges often have small and delicate screws on either side of the cup, which require a fairly light touch. The clutch is perfect for ensuring the right amount of torque is applied and avoiding overdoing it.
Pre-Drilled and Counter Sunk Screws
When using pre-drilled and counter sunk screws, it is important to choose the right clutch setting. Starting with the minimal amount of torque and working up to find the sweet spot can ensure the threads grab onto the surrounding fibers of wood without causing any damage. By using the right clutch setting, the screw can be driven in perfectly flush every single time.
The clutch collar is an essential tool for any power drill user. By understanding how it functions mechanically on the inside, users can know when to use it, how to use it, and how it compares from one drill manufacturer to another. With different drive settings available on different drills, it is important to know how to choose the right clutch setting. Whether one is totally new to power tools or super experienced, there are always new things to learn about the clutch.
Internal Mechanics of the Clutch
The clutch collar is an essential component of a power drill, and it is crucial to understand how it works. The clutch collar is responsible for controlling the torque output of the drill, which is important when driving screws or fasteners. The clutch settings vary depending on the drill, and it is important to use the correct setting for the task at hand.
The clutch collar is a mechanical device that operates using a spring. The spring compresses when the collar is turned, creating resistance that limits the amount of torque that the drill can produce. The higher the clutch setting, the more resistance there is, and the less torque the drill will produce.
One of the benefits of the clutch is that it allows for more delicate work, such as driving small screws. When working with smaller screws, it is important to use a lower clutch setting to avoid stripping the screw or damaging the surrounding material. The clutch is also useful when working with pre-drilled and pre-countersunk screws, as it allows for precise control over the depth of the screw.
The clutch collar has been around for over 75 years and was invented by Black & Decker. The mechanics of the clutch have not changed much since its invention, and it remains an essential component of power drills today.
To understand how the clutch works, it is helpful to take a look inside the drill. The clutch operates using a spring, which compresses when the collar is turned. The spring creates resistance, which limits the amount of torque that the drill can produce. The higher the clutch setting, the more resistance there is, and the less torque the drill will produce.
In conclusion, the clutch collar is an important component of a power drill, and it is crucial to understand how it works. Using the correct clutch setting for the task at hand will ensure that the drill operates efficiently and effectively.
Historical Facts about the Clutch
Invention of the Clutch
The pistol grip or drill style that we know today with a trigger and everything has been around for over 100 years, but the clutch was actually invented over 75 years ago by Black & Decker, which is now called Stanley Black and Decker. The clutch hasn’t changed much since its invention in 1946. It is a version of the clutch collar that is found on most drills today.
Black & Decker’s Contribution
Black & Decker has been a major player in the power tool industry for decades and their contribution to the invention of the clutch cannot be overstated. They own several other brands such as DeWalt, Porter Cable, and Craftsman. The clutch is a mechanism that allows users to adjust the amount of torque that is applied to a screw or fastener. It is designed to prevent the user from overdriving a screw or damaging the surrounding material.
The clutch is an essential feature on power drills and impact drivers. It is particularly useful when working with delicate materials or smaller screws. The clutch settings can be adjusted depending on the size of the screw and the material being used. It is recommended to start with the minimal amount of torque and work your way up to find the sweet spot.
The clutch works by using a spring inside the collar that compresses and gives resistance as the user turns the collar. The higher the setting, the more resistance the spring provides, resulting in more torque being applied to the screw or fastener.
In conclusion, the clutch is an important feature on power drills and impact drivers that has been around for over 75 years. It was invented by Black & Decker and has remained relatively unchanged since its inception. The clutch allows users to adjust the amount of torque that is applied to a screw or fastener, making it an essential tool for any DIY enthusiast or professional contractor.
Disassembling the Drill to Examine the Clutch
The clutch is an essential component of a power drill that allows the user to control the amount of torque applied to the fastener. By adjusting the clutch settings, the user can prevent overdriving or stripping the screw or damaging the workpiece. In this section, we will explore the mechanics of the clutch and how it functions inside the drill.
To gain a better understanding of the clutch, the speaker in the video disassembles a drill to show its internal components. The clutch collar is the outermost part of the clutch mechanism that rotates around the drill chuck. The collar has several numbered graduations that correspond to the different clutch settings, ranging from low to high torque.
The speaker explains that the clutch should only be used when driving screws or fasteners of some sort. Using the example of driving screws into a Douglas fir 4×4, the speaker demonstrates how the torque applied to the screws varies with each clutch setting. The clutch settings are particularly useful when working with delicate screws, such as those used in cabinet hardware or cup hinges. By using a lighter clutch setting, the user can avoid overdriving the screws and damaging the workpiece.
The speaker also shares some interesting facts about the clutch, such as its invention by Black & Decker in 1946 and how it has remained largely unchanged since then. To further illustrate how the clutch works, the speaker disassembles a drill and shows the spring inside the clutch collar that provides the resistance when turning the collar.
In summary, the clutch is a crucial component of a power drill that allows the user to control the amount of torque applied to the fastener. By adjusting the clutch settings, the user can prevent overdriving or stripping the screw and damaging the workpiece. The mechanics of the clutch are relatively simple, with a spring inside the clutch collar providing the resistance when turning the collar.
Mechanics of the Clutch Spring
The clutch collar is an essential component of a drill that controls the torque output. The clutch settings vary depending on the drill, and each setting corresponds to a specific torque output. The clutch collar contains a spring that compresses and provides resistance when the collar is turned. The resistance from the spring determines the amount of torque that the drill produces.
The clutch collar is designed to be used when driving screws or fasteners. It is not intended for use when drilling holes. The clutch settings are particularly useful when working with delicate materials or smaller screws that require a lighter touch. For example, when installing cabinet hardware or cup hinges, a lighter clutch setting is necessary to prevent stripping out the screw or the screw hole.
Inside the clutch collar, there is a spring that compresses and provides resistance when the collar is turned. The amount of resistance from the spring determines the torque output of the drill. The clutch collar has been around for over 75 years since it was invented by Black & Decker in 1946. The mechanics of the clutch collar have not changed much since its invention.
In summary, the clutch collar plays a crucial role in controlling the torque output of a drill. It is particularly useful when working with delicate materials or smaller screws that require a lighter touch. The mechanics of the clutch collar are relatively simple, with a spring providing resistance when the collar is turned.